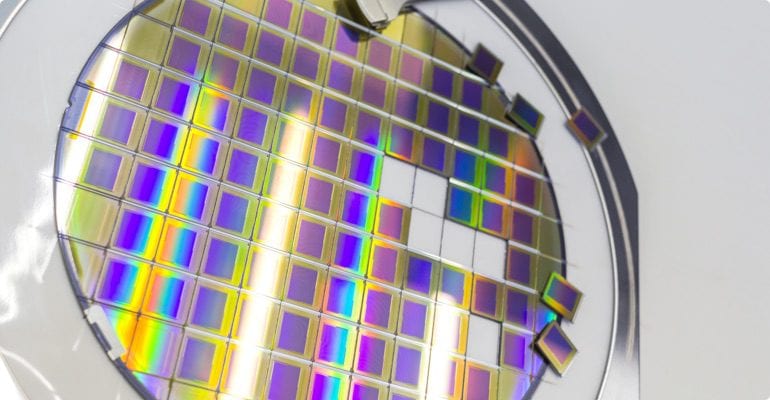
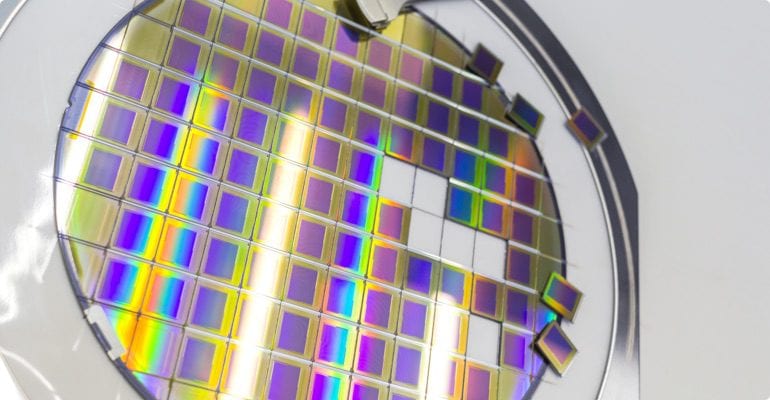
The Orthogonal process is compatible with existing TFT backplanes used with OLED today.
Used to define the active pixel areas. Due to the increased registration accuracy, the fill factor of the pixels can be greatly increased without risk of color mixing.
The fluorinated Sacrificial Layer acts to planarize and release cleanly from the surface during the delamination step, leaving no residue behind. Sacrificial Layer can be coated through typical wet-coating processes like spin coating or slot-die coating.
The Photoresist Layer is Orthogonal’s fluorinated photoresist polymer. It is a negative tone resist, sensitive at i-line wavelengths (365nm) and is solution coated similar to the Sacrificial Layer material.
Using standard lithographic exposure tools, the pixel patterns for the first color are defined in the Photoresist Layer.
Using OLED-safe fluorinated developers, the Photoresist Layer pattern is developed with the material in the pixel holes getting washed away.
Using a separate fluorinated developer formulation, windows in the Sacrificial Layer layer are opened and an undercut profile is formed.
Deposit the OLED materials in a standard VTE system with open frame masks (no FMM needed!).
Sacrificial Layer layer is cleanly dissolved in a fluorosolvent and the top resist is removed cleanly, without leaving small particles.
Pattern the next two colors the same way.
Deposit the final layers through the cathode in the usual way and encapsulate.